The Challenge
Virtual production monitoring and control with real-time location tracking and dynamic E-Ink displays
Operating in more than 90 countries and with 90,000 employees worldwide, this global leader and provider of reliable energy products supports its customers on their way to a sustainable future.
This company was looking to optimize operations along their entire energy chain. Our client’s production processes include a high-value powder used in 3D printers for additive manufacturing. Using this powder for the production of various parts involves several intensive processing methods and steps. Containers and hoppers holding this powder pass through multiple stations and undergo numerous quality tests. This requires real-time visibility and time-sensitive status updates, recording, and booking of the various containers throughout the entire production process.
Monitoring all this with outdated paper-based methods was very time consuming and error prone for employees. Additionally, the production process extends over several zones and buildings, and the individual stations could only be monitored by manual recording. Detection of important events like if a container is ready for pickup or if a process step deviates from production specifications may only be likely when delays or issues become especially glaring. Production zones are also subject to certain safety regulations, so entry or further processing may only be carried out by authorized personnel.
The company's goal was to digitize the individual production steps and create the most efficient utilization of resources while maintaining high quality and safety standards. To deliver on these goals, the company turned to Inpixon’s INTRANAV smart factory solution, implementing a RTLS solution that delivered real-time location visibility for powder containers, automated workflows interacting with electronic displays, and analytics.
Customer Requirements
Real-time alerts in case of process deviations
Enable real-time location and status updates with platform-based notifications as soon as predefined processes deviate from target values.
Workflow optimization through process and material flow analyses
Leverage analytics into the location and movements of tagged assets to enhance workflows through optimization of parameters such as dwell times, idle times, throughput times, and trails as structured data exports via CSV.
Location and batch tracking of powder containers
Visualize ongoing production processes with centimeter-level precision through UWB real-time location tracking and digital mapping of powder containers for additive manufacturing.
Initiation of follow-up processes through geofence-based workflows
Leverage geofence-based notifications with event triggers for instances such as process blockers, process releases or notifications for ready-to-go internal transports.
Paperless factory: real-time status updates through E-Ink displays
Implement a paperless factory with real-time status updates via E-Ink displays that show important production details such as status, material number, batch number, batch barcode, quantity, SAP material number, number of reuses, powder container, and container type.
Quality locking and authorization
Leverage location-based information to lock or unlock processes through integration with the SAP MES interface.
IoT Requirements
Data transfer and interaction from cloud to local edge
Interaction between RTLS TAG and the E-Ink display
Interface to the Mendix App and SAP
INTRANAV Real-Time Digital Twin
Mapping powder container flow through production for additive manufacturing
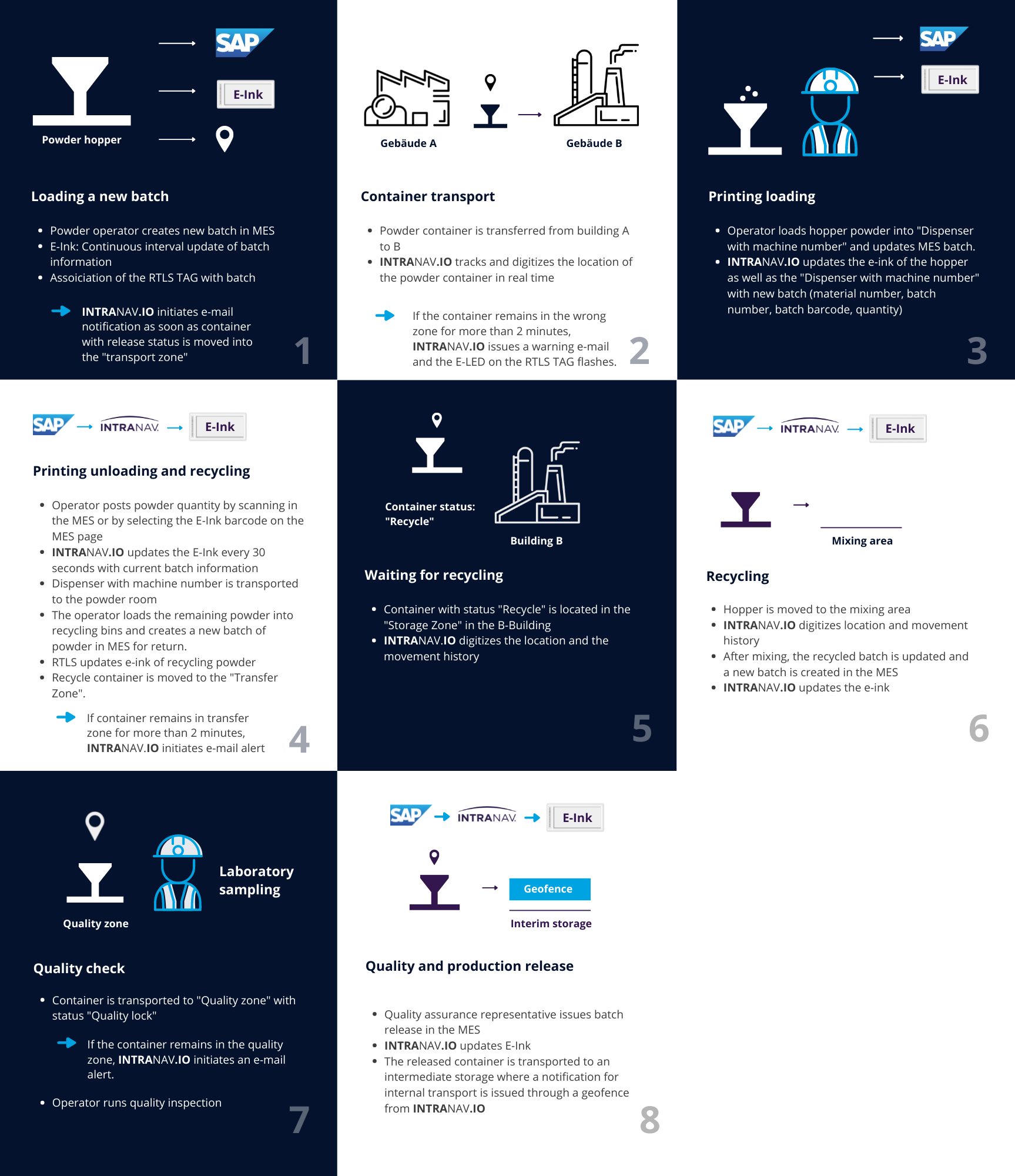
The Solution
The key to monitoring real-time material flow and production status as the powder moved throughout the client’s manufacturing processes, reducing manual, error-prone processes and enabling 100% paperless production was to use Inpixon’s INTRANAV IoT platform, RTLS, and dynamic E-Ink displays.
How the energy company uses Inpixon's RTLS solution in its powder tracking process
Loading a New Batch
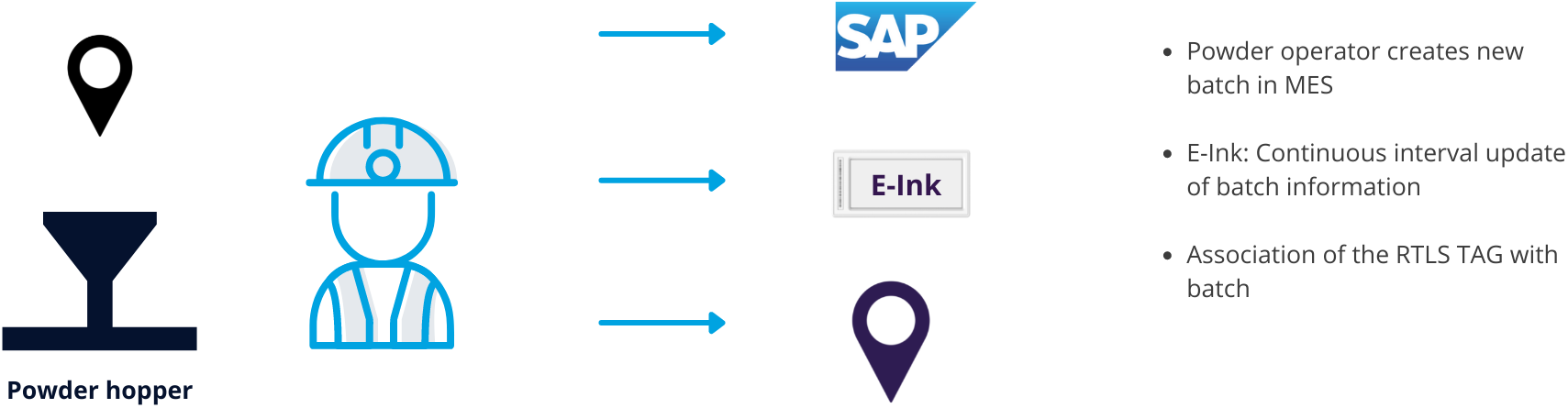
-
Powder handler creates new batches in MES
-
Within an interval of 30 seconds, the E-ink display is updated with the new batch information (material number, batch number, batch barcode, quantity, batch status, container ID).
Alternative via manual update: The powder plater hits the integration function button on the E-Ink display and thereby triggers the update of the displayed content.
➜
Process assurance: If the
RTLS could not find the correct container ID from the system for the batch number (due to incorrect entry), INTRANAV.IO issues an error alert to the administrator.
Transport Request and Transfer
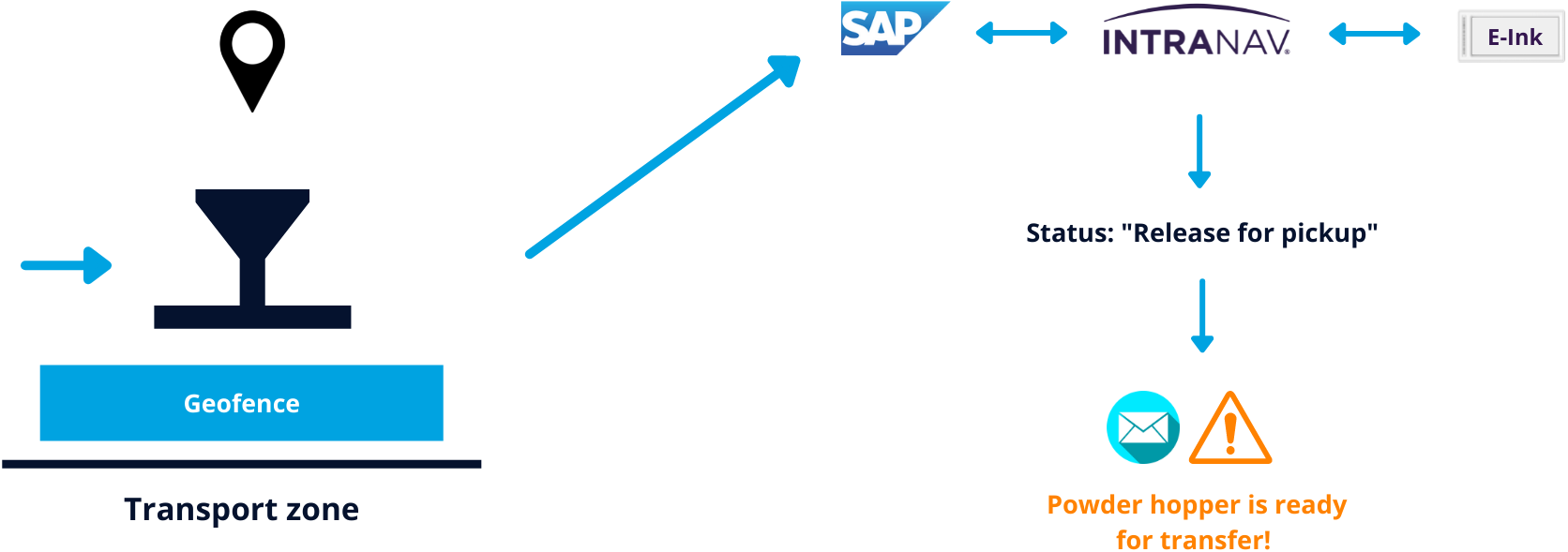
Transfer request
- If the container with the release status is moved to the “Transport Zone”, INTRANAV.IO initiates an e-mail notification.
- The operator could use the report to check the position of the powder containers in the map with different filters (status, material number, container ID, batch number).
➜ Process control: If the container with incorrect status (e.g., Status Not Authorized, Quantity Does Not Correspond to Pre-Set KG, etc.) remains in the transport zone for two minutes, INTRANAV.IO initiates an alert e-mail notification, and the LED flashes red until the container is moved from the defined zones.
Transfer
- The operator physically transfers the released container from the transfer zone in Building A to the designated area in Building B.
- Location and movements are tracked by INTRANAV.IO.
➜ Process reliability: If the hopper remains in the wrong zone for two minutes, INTRANAV.IO triggers an alert e-mail and a flashing of the E-LED.
Printing Loading
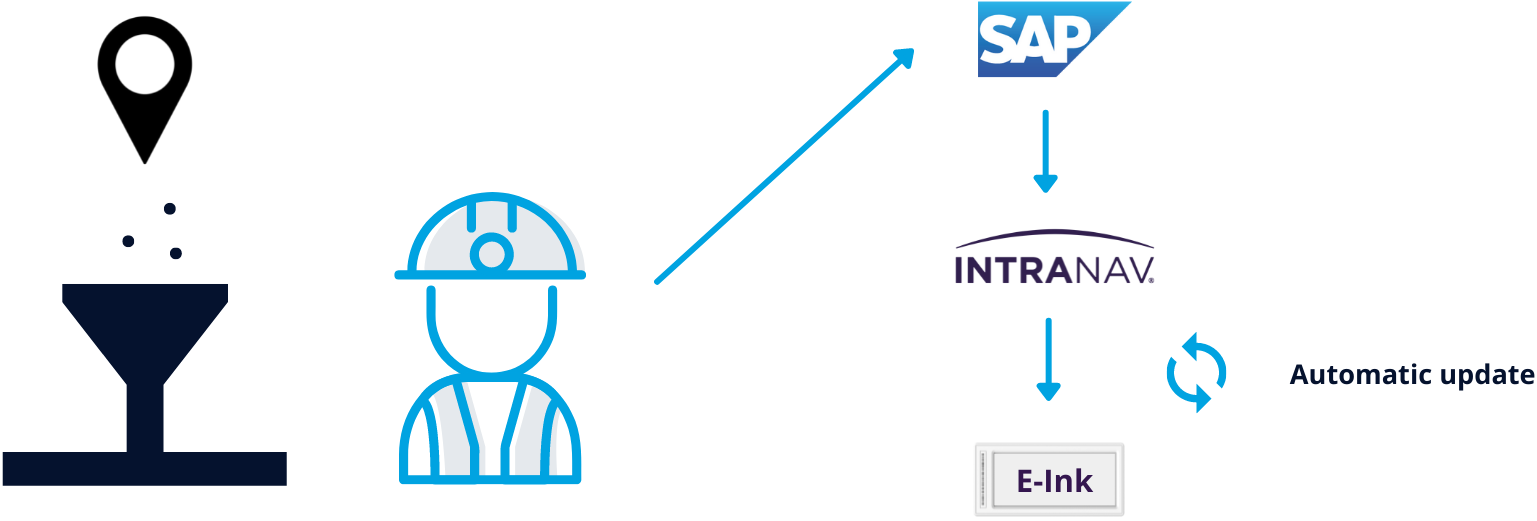
- The operator loads hopper powder into the dispenser with machine number and updates MES batch.
- INTRANAV.IO updates the hopper E-Ink display and the dispenser with the new batch (material number, batch number, batch barcode, quantity).
Manual operation: The operator initiates the update of the E-Ink display by pushing the function key to update the E-Ink.
Printing Unloading
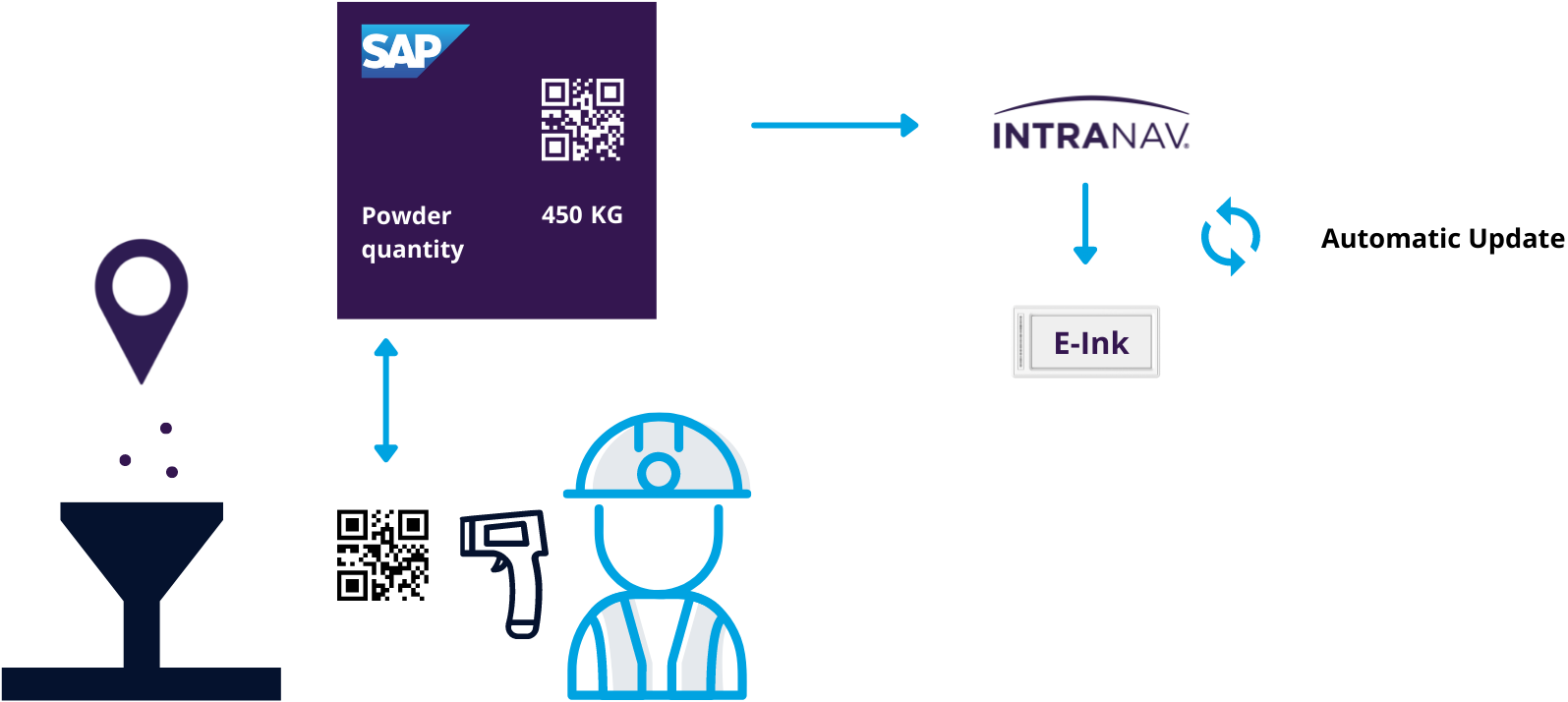
When the print job is finished, the operator posts the corresponding powder quantity by scanning in the MES or manually selects the E-Ink barcode via the MES powder consumption page.
- INTRANAV.IO updates the batch information of the E-Ink every 30 seconds. Alternatively, this can be initiated manually via the function key on the E-Ink display.
- The dispenser is transported into the “Powder Area”.
- The operator loads the remaining powder into the recycling container. The operator then creates a new batch of powder in the MES for recycling.
- INTRANAV.IO updates the E-Ink display of the recycling powder (with status “In Use”).
➜ Process control: When the production hopper is moved in the recycling zone, the RTLS initiates blinking of the E-Ink display for alerts. Reverse for recycling hopper.
Transfer Request
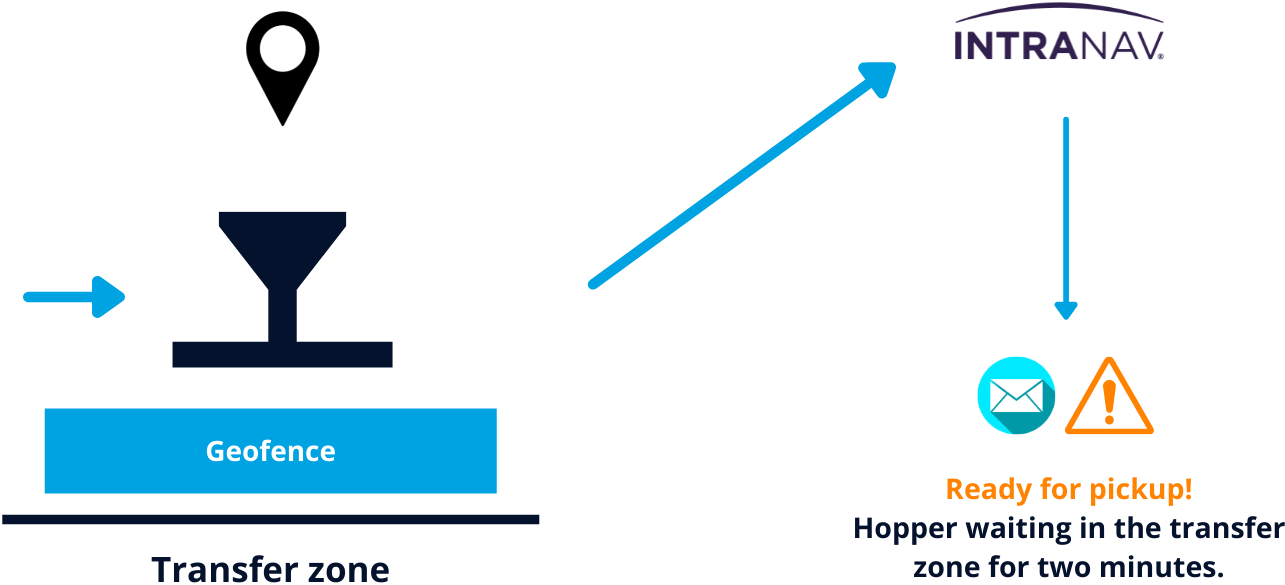
- The recycle bin is moved to the “Transfer Zone”.
➜ Process control: INTRANAV.IO initiates an e-mail notification if the hopper remains in the “Transfer Zone” for two minutes.
Recycling
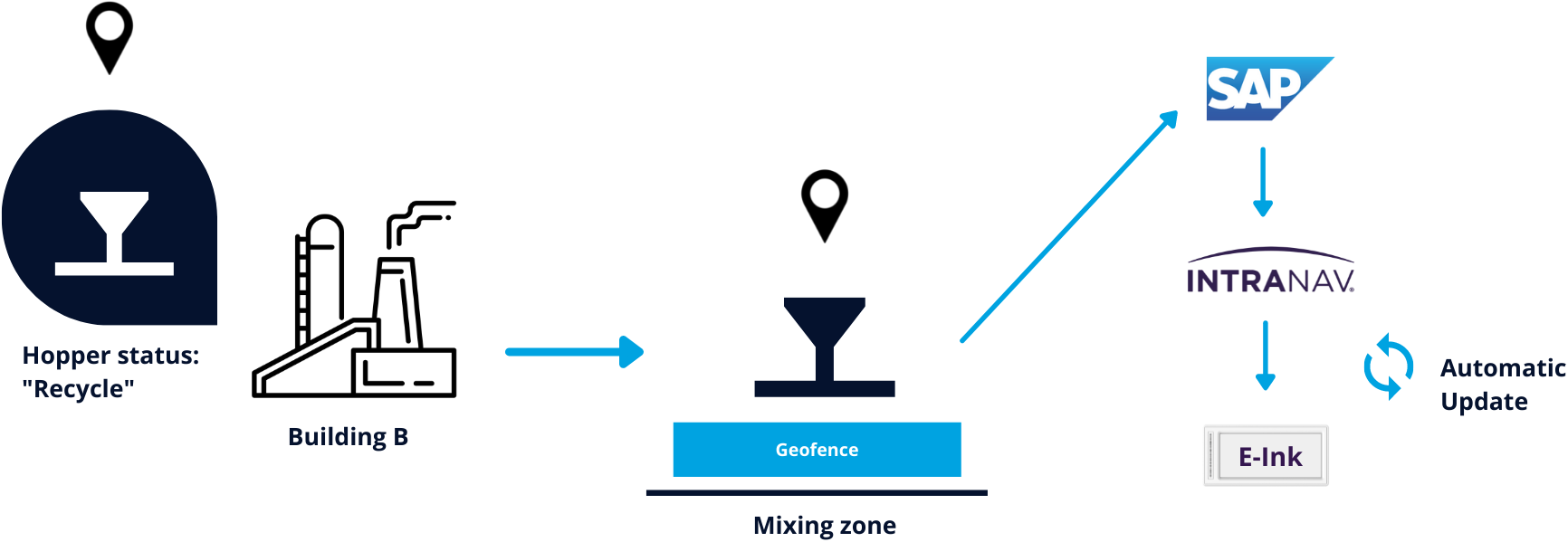
- Container with status “Recycle” is located in the “Storage Zone” in Building B, INTRANAV.IO tracks the location and movement history.
- Hoppers are moved to the mixing area, INTRANAV.IO tracks location and movement history.
- After mixing, the recycled batch is updated and a new batch is created to match it in the MES (new batches with the status “Quality Lock”).
- INTRANAV.IO updates the E-Ink display according to how it was defined in the previous steps.
Quality Check
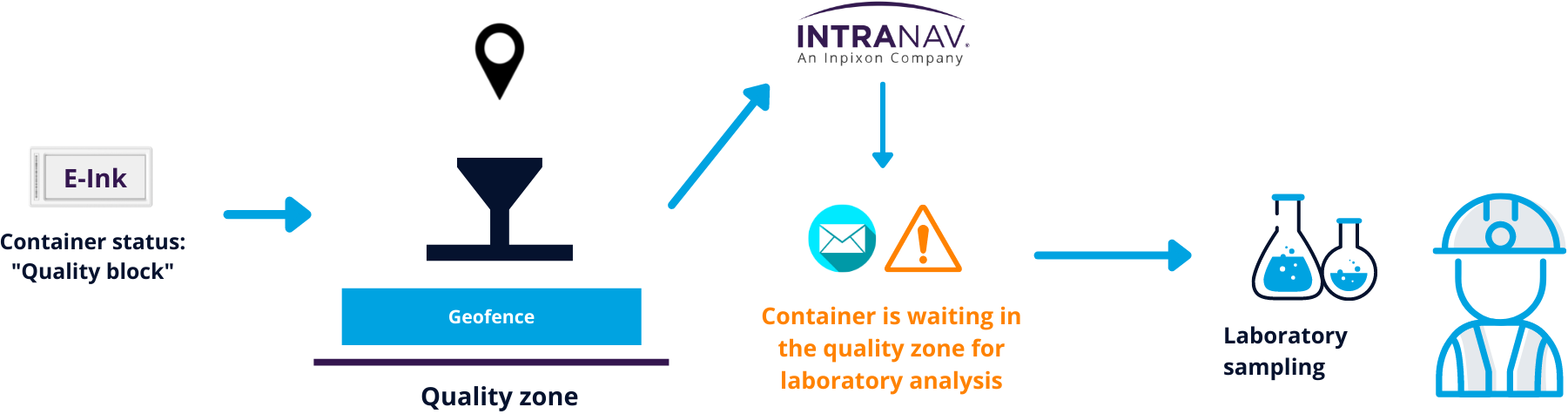
- Operator moves the container with status “Quality Lock” to the “Quality Zone”.
- When the container stops in the “Quality Zone”, INTRANAV.IO initiates an e-mail notification.
- Quality operator removes the sample from the hopper and carries out the powder test in the QMS.
Quality and Production Release
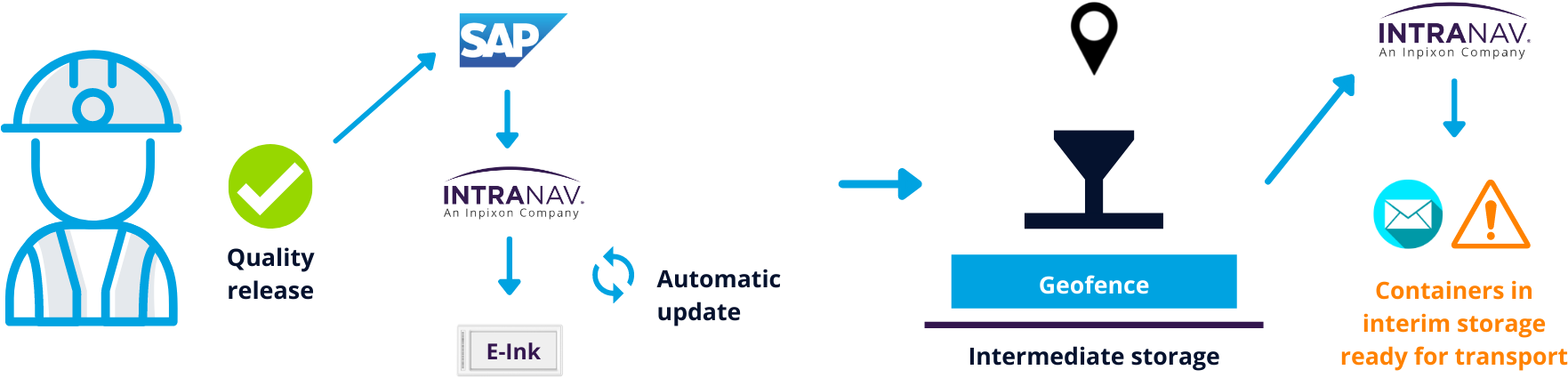
- Quality manager releases the batch in the MES and INTRANAV.IO will refresh the E-Ink display accordingly.
- The “Released” containers are moved to the interim storage, which initiates the notification for internal transport.
The Result
Summary of the results achieved by our customer:
- With real-time location tracking of powder containers via the RTLS platform, the energy company monitors the real-time status of all production steps including downtimes and interruptions. Errors in the process flow can instantly be identified and remediated.
- The interaction between RTLS and E-Ink displays enabled the transition to a digital, paperless factory, eliminating all manual data entry efforts and removing the need for manual updates. The batch/status updates of the E-Ink displays are performed automatically by the real-time location of the container.
- Real-time notifications of the current production status, such as “Dwell Time Too Long in One Zone”, “Container is Ready for Pickup” or “ Container Located in the Quality Zone”, ensure production processes adhere to quality and completion time standards.
- Real-time alerts (e.g., if the containers have been transferred to the wrong zone or an indication of a manually required interaction) enable fast intervention in the event of process deviations in order to avoid long waiting times and interruptions to production flow.
- Automated workflows initiate follow-up processes, such as blocking safety zones (quality blocking or release) or initiating pickup orders.
- Material flow and resource utilization analytics, flow status information, structured data export via CSV, and the associated integration in analytics tools such as Power-BI, provide visibility into downtimes, idling and throughput times, and zone occupancy periods as well as utilization. For this purpose, INTRANAV.IO records the exact timestamp (day / hour : minute : second) for entrance and exit of respective zones and calculates, for example, the dwell time in the respective zone to the second. The output is a reading of the total throughput time of all zones and intermediate transit times per asset/package/material flow relationship. Extensive process optimizations in the production flow can be carried out based on the historical data of the completed transports and the idle times of the containers at the passed zones.
E-Ink Displays for Paperless Logistics and Production
E-Ink displays can drastically improve logistics and manufacturing processes through access to dynamic operational intelligence. In combination with our INTRANAV.IO platform, customers can send location-based information and instructions to the E-Ink display to automate and optimize processes on the shop floor or in the warehouse. Users can create workflows, rules and generate content depending on real-time information for how production processes are unfolding. (E-Ink tags are a third-party product that works seamlessly with the INTRANAV solution).
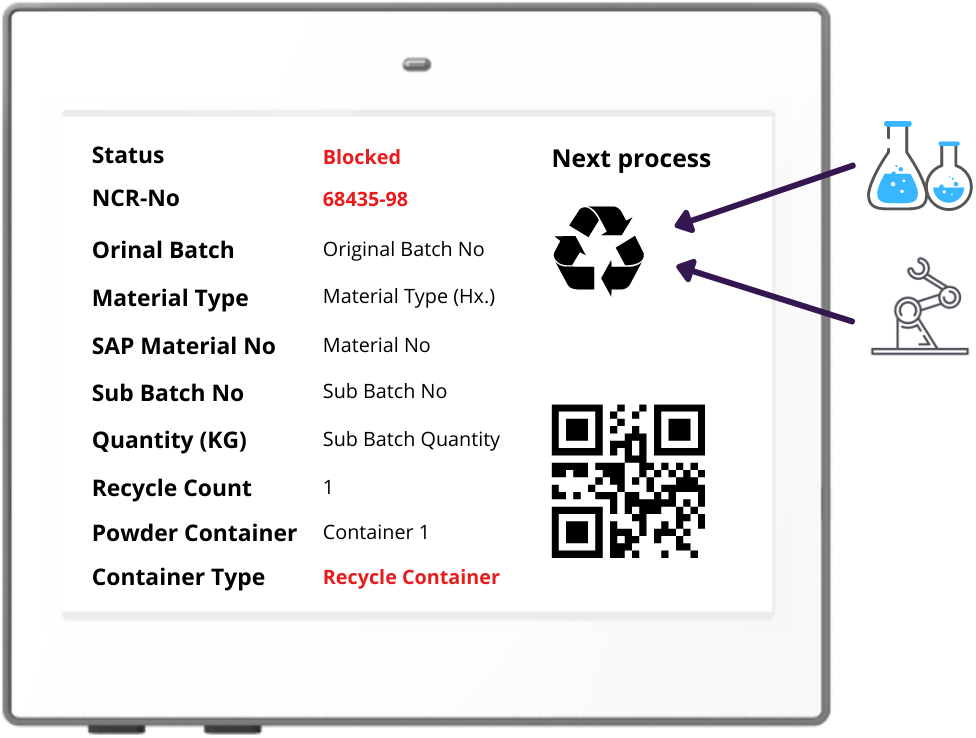
Our software suite offers a broad portfolio of pre-built E-Ink applications:
- Dynamic information for inventory & asset flow control
- Real-time assembly line & manufacturing management
- Dynamic picking and item lists updated by events and order information
- ERP / WMS / MES interfaces to visualize critical information as changes occur
- E-Kanban via integrated device buttons
- Real-time track & trace with additional information and work instructions
- Pick-by-light for faster picking in the warehouse and at the assembly line
- Machine information and order progress
Key Benefits
- 100% process transparency through digitization and monitoring of the actual manufacturing process and the flow of powder containers throughout it
- Paperless handling eliminates manual data entry efforts and frees up worker time for higher-value activities
- Increased workflow reliability through KPI monitoring, alerts and automatic process blocking and release
- Real-time process triggers reduce manual effort and ensure timely compliance with processes parameters
- Reduction of search times through real-time material visibility
- Minimization of process deviations
- Optimization of resource and capacity utilization to enhance lean production:
- Reduction of downtimes, throughput times, detours, and process waste.
- Efficient route planning, production capacity utilization, area utilization, and optimization of production layout
If our INTRANAV smart factory solution is of interest to you, contact us to discuss optimization possibilities for your manufacturing and logistics workflows today!