Real-time location systems are used by industry leaders all over the world for operational awareness and improved working conditions, thanks to the functionality of indoor data. Chirp Spread Spectrum (CSS), also known as chirp, is a powerful 3-in-1 technology that enables ranging, communication and tracking. It’s a suitable radio frequency (RF) technology for many different safety scenarios because of its unique ability to work over long ranges outdoors and its strong protection against interference. In this post, we’ll go over some key ways chirp can improve safety in industrial settings.
Safety Application #1: Collision Avoidance & Awareness
Collision Awareness
In dangerous industrial environments, near collisions happen daily. Whether it's between multiple vehicles or a vehicle and a person, investing in a collision awareness system (CAS) can help protect heavy equipment operators, on-site personnel, contractors and valuable equipment.
Compared to other radio-frequency technologies, chirp works well outdoors, has long ranging abilities, and has strong protection against interference, making it a great match in industrial environments. When all equipment and personnel are tagged, a chirp-enabled CAS works using two-way ranging (TWR). This way when tagged devices are in close proximity, they can alert each other, either through an audio message, a light flashing display color changes, vibrations etc., so action can be taken before a collision occurs.
With collision avoidance, the most important benefit is improving overall safety for employees and contractors, avoiding injuries and death. Organizations can also avoid costs that come with extra downtime, investigation shutdowns, and equipment damage and loss.
Collision Avoidance
Collision avoidance systems have similar use cases to collision awareness, with the goal of preventing accidents. The main difference is that while collision awareness warns people of proximity and with this the driver has to prevent the accident by breaking by themselves, collision avoidance systems are set in place to stop vehicles from moving once they get too close automatically without the need of a driver interaction. This can be needed in situations where workers fall asleep, get distracted or become incapable of operating a vehicle. So when all equipment and people are tagged and a vehicle gets too close, it will be forced to stop in place, preventing any human error.
This requires a few more steps to implement than collision awareness, including the need for vehicle automation via systems such as the CAN Bus and regulatory compliance since the vehicles will be automated. The human operated vehicles also need to be retrofitted with a digital/mechanical brake or steering actuation, to stop the vehicle automatically. With that, along with increased safety and reduced accident costs, a great advantage of a collision avoidance system is that humans are not required to stop the vehicles.
Key Considerations for Collision Avoidance & Awareness
- Knowing what positioning and tracking infrastructure and pre-existing RF technologies have already been installed is required
- Understanding if you need a vehicle-to-person (V2P) or vehicle-to-vehicle (V2V) CAS
- The importance of low latency for faster reaction time and calculating maximum speed thresholds for brake paths
- The need for an audio/visual conditional alarm, instead of a warning message
- Meeting regulatory specifications for the country you’re operating in
- The need for false positive alarms to be filtered
- Calculating the distance and speed to objects beforehand, to activate the avoidance algorithm
Safety Application #2: Operational Awareness for Remote-Controlled Shovels, Containers and Cranes
On a daily basis, large vehicles and machines such as shovels, dozers, cranes etc., are operating near each other and personnel, and almost collide due to blind spots. Because of this, shovel operators that use a remote controller to perform vehicle functions can benefit from a collision awareness system that increases communication between shovel and dozer operators, greatly reducing the number of accidents that happen.
When large vehicles and workers using the remote-control devices are tagged, the workers can be protected from accidentally running themselves over by these large vehicles, especially if they’re controlling multiple vehicles at the same time. This has a range of benefits, from preventing injury and death, avoiding loss of equipment and preventing loss of operational time that happens because of those situations.
Key Considerations for Operational Awareness for Remote-Controlled Shovels, Containers and Cranes
- Shovel operators must be able to get both visual and audio alerts that a dozer or other vehicle is in its blind spot when in a bucket swing
- Dozers or other vehicles must be able to get both visual and audio alerts that they are in the shovel’s blind spot
Safety Application #3: Autonomous Processes
Autonomous processes in environments like mines, warehouses or factories – where manual processes are replaced with automated vehicles or equipment - require reliable positioning for the highest accuracy possible. Leveraging RTLS location data for automation means that fewer workers are required for high-risk operations, and more accidents can be prevented.
In many cases, GPS is available above ground but never underground, and it requires a base station and server causing high latency and even loss of signal at times. When this happens, GPS tracking isn’t as accurate as it may show a machine is at a position after it has already left. In this scenario, chirp is a great match as it works reliably outdoors and indoors, over long ranges and provides location accuracy of 1-2 meters which works well with the kind of large assets being tracked in these environments. Chirp can also be deployed along with GPS to provide an extra layer of reliability if GPS fails. In addition, even when GPS is being used, a chirp RTLS can provide information on a vehicle’s speed if other systems such as the CAN Bus is not in place.
So for autonomous processes, assets can be tagged for the location tracking of every person, vehicle and machine to stay accountable, and the tags can also be enabled for TWR if needed between vehicles or people. Using radio positioning equipment with chirp also provides a location with low latency and is lightweight compared to GPS.
Key Considerations for Autonomous Processes
- How accurate the positioning needs to be
- Knowing what positioning and tracking infrastructure is required, including a radio frequency positioning system
- Understanding if you need vehicle-to-person (V2P) or vehicle-to-vehicle (V2V) ranging, or both
- The importance of low latency for faster reaction time
- Calculating the distance and speed to objects beforehand, to activate the avoidance algorithm
Safety Application #4: Location Tracking
Operational Tracking
Tracking personnel in industrial or dangerous environments is key to keeping everyone safe and staying accountable for all workers and contractors. People are put in dangerous scenarios every day, so the need for an RTLS to track employees is high. The reliability of a chirp-enabled RTLS helps organizations stay secure, by allowing personnel and assets to be tagged and tracked even in harsh industrial environments like, factories, mines and process plants. This location data can then be used to see exactly where everything is on a digitized facility map.
The benefits to having operational tracking in different facilities are the visibility over operations, meeting regulations such as rules e.g., under the Mine Safety and Health Administration (MSHA), and being able to gain data on how to make processes more efficient.
Safety Incident Investigation Forensic Replay
When accidents happen, it’s useful to have location data to be able to find the cause of the accident, and prevent it in the future. When assets and personnel are tracked with an RTLS, it enables forensic replay to be able to track what events happened and when. Without this information, investigations can take a while which only costs more money since production is being shut down.
The general benefits of using chirp for safety incidents are having time stamped events from integrated systems which help minimize investigation time, being able to perform a Root Cause Analysis (RCA), and having the option of doing an operational review which allows a mine (or other industrial site) to change its operations and improve productivity and safety.
Safety Exclusion Zones
Safety exclusion zones are used in hazardous areas of industrial settings to prevent anyone from entering them. Using geofencing, virtual perimeters are created which trigger alerts and actions when a tagged person or object comes near, ensuring that they don’t go into the zone. These zones can track the proximity of vehicle/worker, vehicle/vehicle, worker/heavy machinery and either send a warning or automatically stop a vehicle, depending on which CAS is being used.
With chirp, these zones can be as large as needed as chirp enables long ranging - and less infrastructure is required, reducing costs. Supervisors can also receive real-time alerts and see on a digitized map exactly what is in the area, if anything has entered the zone and how long for. Zones can also be used to identify theft of valuable equipment by tracking what is entering and leaving the area.
Key Considerations for Location Tracking
- Understanding what tracking infrastructure is required
- Determining the accuracy of location needed
- The need for operational context with location (to correlate operational contextual data with safety related events)
- Safety alerts need to be visual and audio for those being tracked
- Must be able to record a safety related event with a timestamp
Safety Application #5: Blast Safety Awareness & Evacuation
In open pit mining, railway tunnel or road construction, blasts happen on a regular basis to remove and extract rock or minerals from the earth, which can be an incredibly dangerous situation for any mining personnel or contractors in the area. It’s crucial to make sure that no one is near the open pit mine while the blast is happening, so location tracking using chirp is the best match since it works outdoors and can cover large areas.
Since everyone is tracked, on-site supervisors can see on a map exactly where everyone is and check that there are no tagged workers that need to be evacuated from the blast zone. Including this as a step in the security check adds a layer of safety as everyone is alerted to stay clear of the hazardous zone, and prevents any lost time from injuries or damaged equipment.
Key Considerations for Blast Safety Awareness and Evacuation
- What technology is needed to enable tracking in blast areas
- The audio and visual alerts needed for those in the blast area
- How alerts will appear on monitors, showing the blast area status for equipment and humans
Improving Safety with Chirp
With chirp-enabled RTLS and ranging, a layer of protection is added to facilities, saving time, money and lives. Interested in exploring what’s possible with chirp? Contact us today.
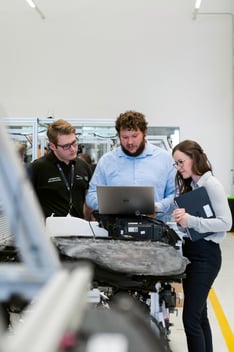